Design and build your own cold air intake
Here’s what you’ll need:
- 180 degree mandrel bent piece of steel pipe – see notes below
- (4) PVC rubber pipe clamps – see notes below
- K&N Funnel Ram Filter – see notes below
- (1) Can of Plasti-Coat High Temperature Ceramic Engine Paint – see remarks below
- 3/8″ ID rubber grommet, 3/8″ OD piece of plastic pipe (approx 4″ pipe), 5/8″ OD (3/8″ ID) piece of vinyl hose (approx 12″ hose) – see notes below
- Flat head screwdriver
- Hacksaw or pneumatic cutting disc
- Electric drill with 3/8″ bit
- Metal file and sandpaper
The total cost of the project is approximately $40 – $60 depending on shipping costs, the brand of filter you purchase, etc.
NOTES:
- Firstly, the hose is a piece of mandrel bent hose. It’s a “180 degree U-bend”. This single piece of pipe will be used to make the entire CAI system. This pipe can be purchased from your local DIY store or on the internet.
- The rubber pipe clamps are also available from any DIY store. They are made from durable, flexible, high temperature black rubber and have (2) stainless steel clamps built in. Go to the PVC plumbing section and look for “PVC Pipe Clamps”. The ones you need are for 2″ pipes, you will need 4 of them.
- On the filter, you will need a cone filter for the end of the pipe to keep the dust out. These cost about $20.00 at your local speed shop. It’s a 6″ filter with a 3″ opening.
- Ceramic paint, go to any Auto Zone or Wal-Mart store and buy “Dupli-Color” brand high temperature engine paint. You will need 1 can.
- The grommet and hoses are used to make the crankcase ventilation system. You can buy the parts at your DIY store when you buy the PCV pipe clips.
Installation Instructions
Please remove the bumper and all stock airbox components.
Removing the bumper and adding an intake
First clean all the pipes, once they’re clean make sure they’re dry. The first step is to cut the pipe. The top bend is the easiest to do first.
As you can see from the picture below, the angle is the same as the stock intake angle. You can use the stock upper section as a rough guide for the cut.
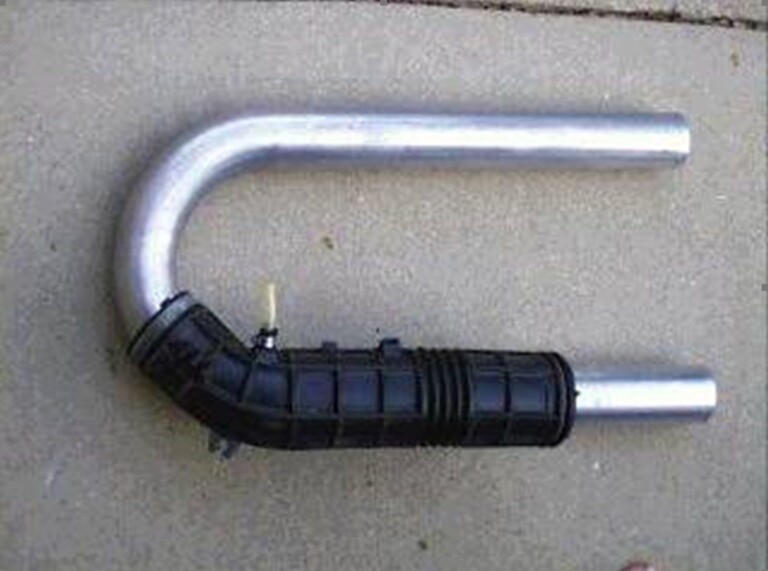
Place the pipe against the throttle body and try to find the right angle at which to cut the pipe.
You’ll need to use your imagination and a little creativity here, but it’s not difficult. See the picture below:
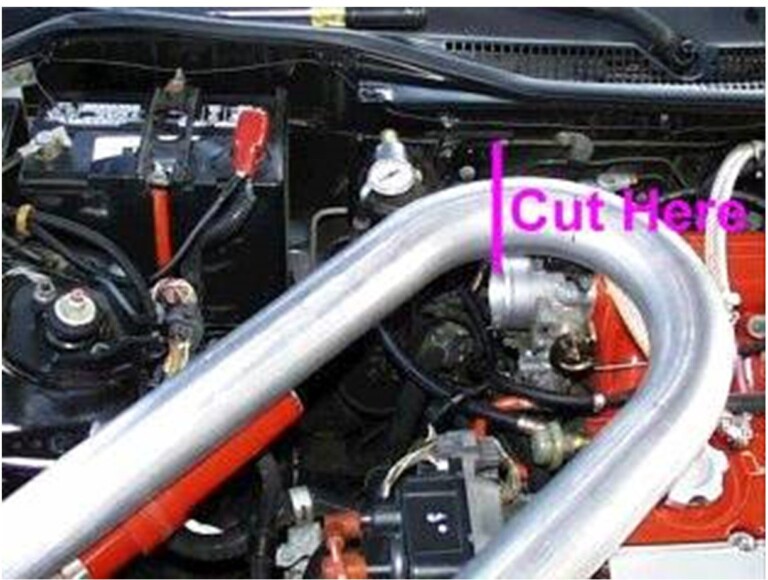
Use a hacksaw or cutting disc to make the cut, making sure it’s straight. When you have finished cutting, use a metal file and sandpaper to remove any rough or sharp edges.
Now check everything by fitting the first rubber tube fitting onto the throttle body. It’s a very tight fit, so it will help to lubricate the fitting with a rubber-friendly lubricant (such as silicone grease or even a little soap). You will have to wrestle it on, but it will fit, as shown in the following picture:
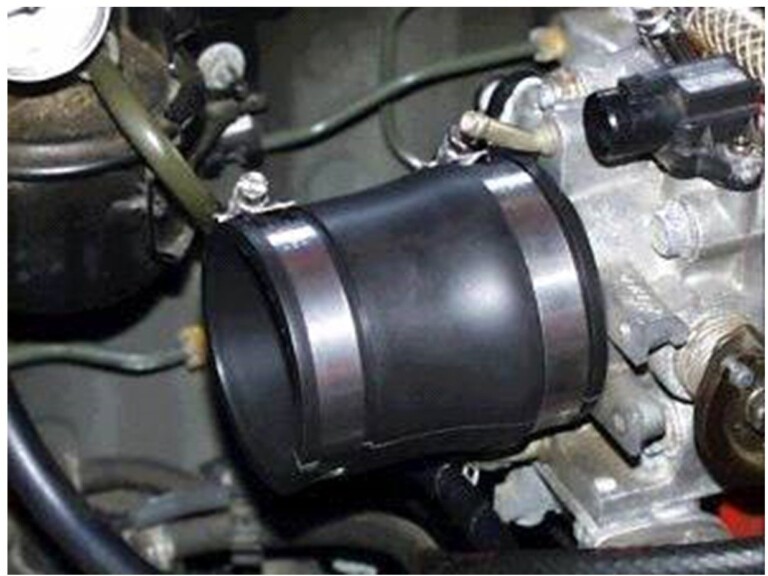
Once you have the fitting in place, insert the pipe and clamp it in place. Make sure that the straight part of the pipe is perfectly aligned with the opening in the bumper where the resonator used to be. One thing to note here. If you are worried about hydrolock and water, you can convert your CAI to a “dry” system by simply screwing the filter onto this short piece of pipe. This is useful during rainy or winter months. See picture below:
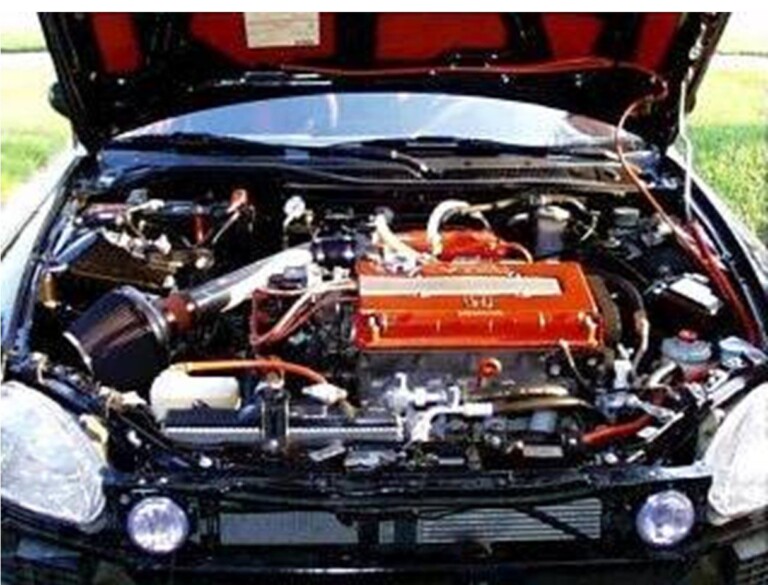
Once you’re happy with the first piece, it’s time to complete the rest of the system. This is where imagination and creativity come into play.
As you make each cut, continue to assemble and test fit the entire intake system. Attach the second tube to the first tube still attached to the throttle body, making sure the second tube bends down into the bumper hole. Then attach the third tube to the second tube and make sure it bends in the opposite direction. You will need to fit the third pipe from inside the lower bumper opening.
Once you have rearranged the pipes, the whole system should look something like the following pictures:
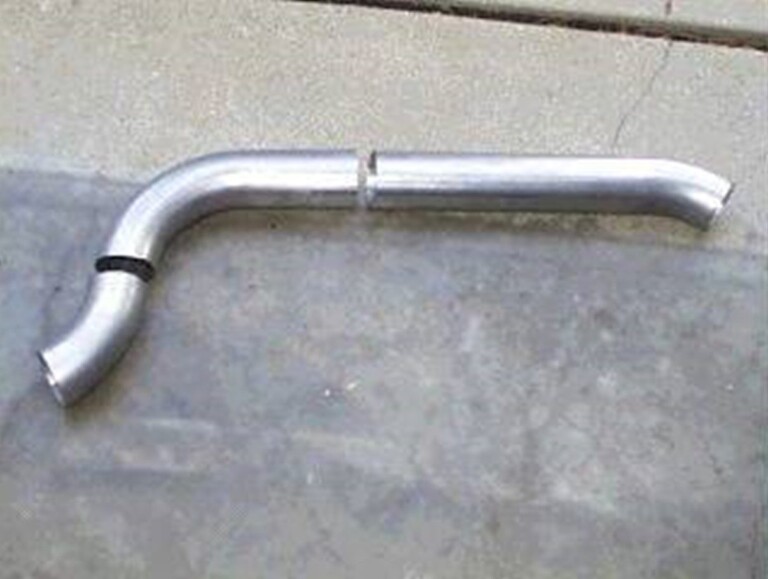
You can assemble the whole system outside the car using the fittings and the filter. It should look like the pictures below:
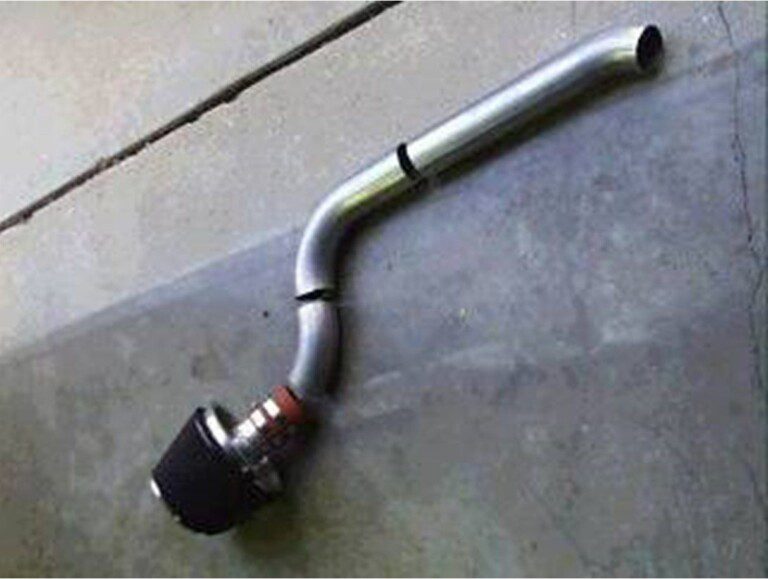
Once the system looks like the pictures and you’ve tested everything, it’s time to finish the job.
This next step is very important.
This step involves making the crankcase breather that goes from the intake system to the valve cover. You must make this part, it cannot be left out! All you need to do is drill a 3/8″ hole in the upper intake manifold. Look at the stock part to see where the hose will go.
It will be easiest to start with a small drill bit and work your way up to 3/8″. Make sure the hole is facing the valve cover connection! Once you have drilled the 3/8″ hole, insert the 3/8″ rubber grommet. Then cut a 3″ or so piece of 3/8″ O.D. plastic tubing and insert it into the grommet. Make sure it is a very tight fit, basically airtight. It may be so tight that you need to lubricate the tube to get it into the grommet. Insert the pipe so that about 1″ is inside the pipe itself and 2″ is outside the pipe. Once the tube is in the pipe, place the 5/8″ OD (3/8″ ID) tube over the tube and attach the other end to the vent on the valve cover. You may need to shorten the length of the tube to fit. Make sure it’s not too tight. But not too much slack either. Also make sure the hose isn’t kinked, as this will restrict airflow.
The following drawing shows how the complete system should look:
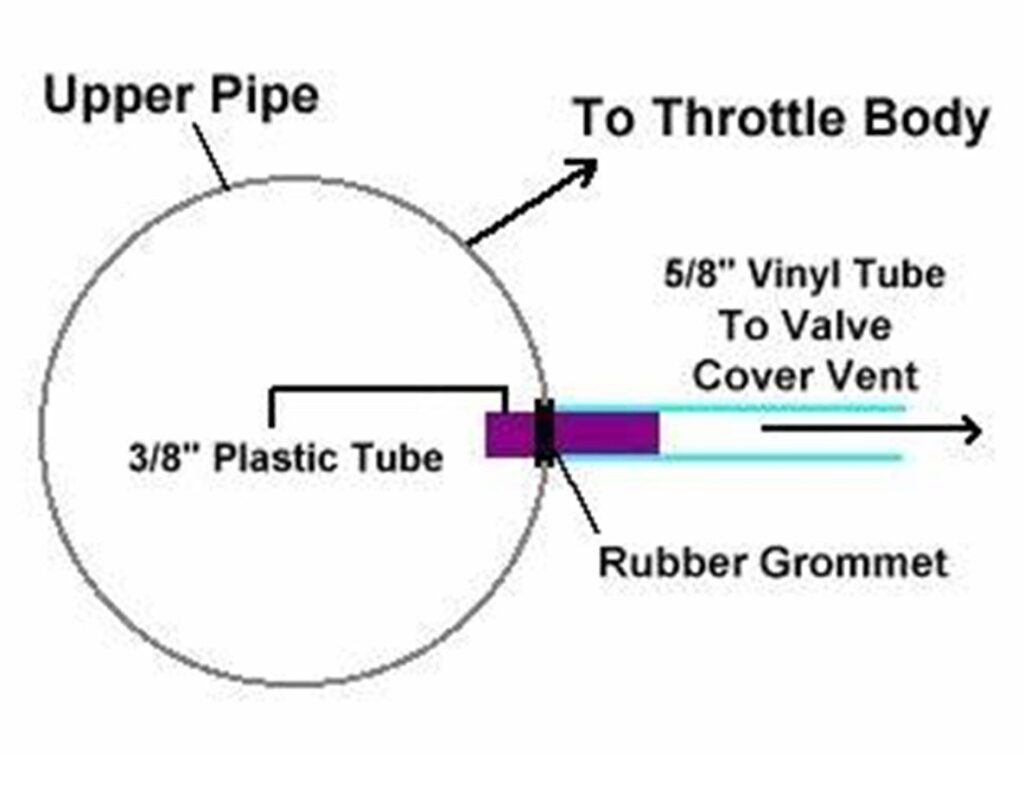
Once the hose system is complete, remove the hose pieces and grommet.
- Note: If you are making this system for an OBD-II car (i.e. 1996+) you will need to make a place for the intake air temperature sensor. See the additional notes section at the end of the article for more information before continuing!
The next step is to paint the system.
Clean everything with soap and water or a good engine degreaser or cleaner. Finally, wipe everything down with isopropyl alcohol to remove any hand and finger grease. Once you’ve done this, it’s time to paint the system. This is a very important step. Why is it important? Well, the pipework is made of plain mild steel, which will rust. The good news is that these pipes have been aluminised because they were originally designed for use as exhaust pipes. This is to our advantage as the aluminisation helps to resist rust caused by rain moisture and winter salt. However, the edges are exposed steel and will rust. Also, the ceramic-based paint will help block most of the engine heat under the bonnet, and painting the inside of the pipe will help smooth the inside. This speeds up airflow, which is a good thing.
YOU WILL BE PAINTING THE INSIDE AND OUTSIDE OF THE PIPING!
Paint the inside of the pipe first, using light coats. You will need to be creative here and spray the inside of the pipe from both ends to ensure that the entire inside of the pipe is covered with paint. Make sure you keep moving the can and don’t spray too hard, as this will cause BAD paint runs and also reduce the overall inside diameter of the pipe. Paint the inside of the system with a total of about 3 light coats.
Allow to dry for a few hours, then come back and clean the outside of the pipe with the isopropyl alcohol to remove any hand or finger oils. Then carefully paint the outside of the pipe with light coats. You will need to turn the pieces over to make sure you cover the whole pipe, or you can just hang the pipe on a piece of string (this will allow you to paint the whole piece at once without having to turn it over to do the other side). Use about 4 coats of paint on the outside.
You will be able to work on the pipe after a few hours or as it dries, but I would HIGHLY recommend letting the paint dry overnight as it takes some time to cure. Follow the instructions on the can of paint for exact details.
Once the system is completely dry, it is time to finish. You will start by CLEANING THE INSIDE OF THE PIPES!!! Anything inside the pipes (i.e. dust, metal shavings, loose paint, etc.) will get sucked RIGHT INTO YOUR ENGINE when you start the car! This is BAD if you haven’t guessed. The easiest way to do this is to feed a medium sized towel into the pipe and pull it out the other end. The towel will pull any loose particles with it, leaving the inside of the pipe clean and ready to go.
Once the pipework has been cleaned, reinstall the grommets and insert the 3/8″ O.D. plastic tube. Then assemble and install the intake system. I had to install the top two pieces first and then bolt on the third piece and filter from underneath the bumper opening. See picture:
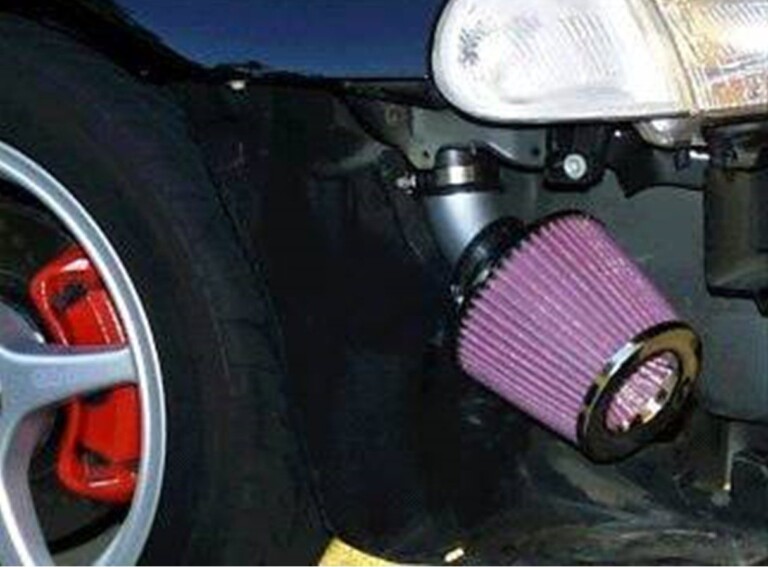
The finished system should look like this:
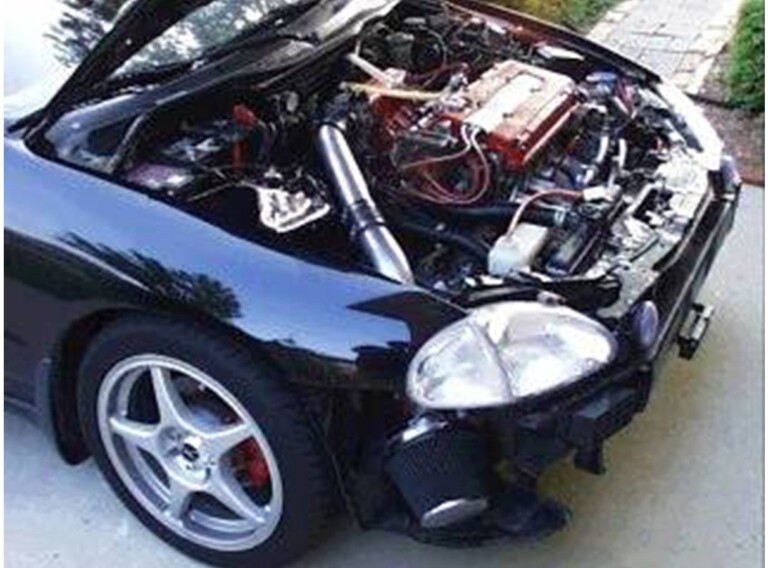
Don’t forget the vinyl tube that goes from the intake manifold to the valve cover vent!
Finally put the bumper back on, clean up and go for a test drive! You should feel a SIGNIFICANT difference in power across the rev range.
ADDITIONAL NOTES:
The above procedure is for OBD-I cars. From 1996 onwards, Honda added a second intake air temperature sensor in the upper intake tube for OBD-II. So if you are installing this system on a 1996+ car, all you need to do is buy an extra grommet and drill a second hole in the intake manifold for the intake temperature sensor. Look at the stock rubber tube to see where the sensor is located and drill the hole in roughly the same place. Then simply insert the grommet and the intake temperature sensor, secure everything and you’re done!
The intake tubes listed are 2.5″. For larger engines (Type R, H-series and even non-intercooled turbocharged cars) you can use 3″ pipes. I would not recommend using the 3″ tubing on smaller engines (like 1.5 and 1.6L etc.) as you will lose a lot of the low and mid-range power that the AEM system was specifically designed for.